Design Services
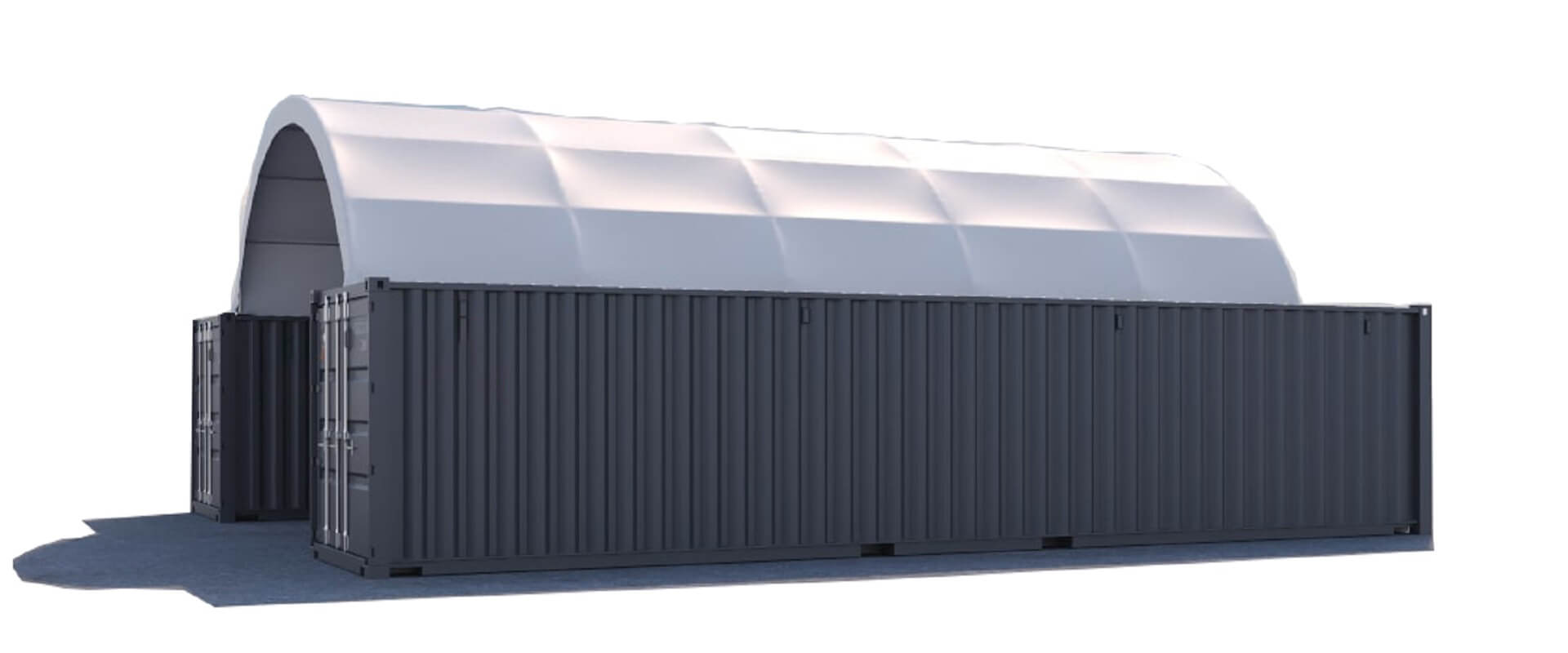
High wind resistance tent with reinforced frame and PVC cover providing heavy-duty storage for industrial applications
PRODUCT PARAMETERS
- Frame Material: Metal
- Frame Finishing: Powder Coated
- Sail Finishing: Pvc Coated
- Durable Fabric Covering: Made from high-strength, weather-resistant materials
- Lightweight Structure: Fabric buildings are considerably lighter than traditional metal
- Quick Installation: Many fabric structures can be erected in a fraction of the time
- Cost-Effective: Lower maintenance costs over time compared to traditional buildings
- Natural Light: The translucent nature of the fabric allows natural light to enter
- Ventilation Options: Many fabric buildings can be equipped with ventilation systems
- Customizable Sizes andConfigurations: Available in a variety of sizes and can be customized
- Energy Efficiency: The ability to utilize natural light can contribute to energy savings
- Versatile Applications: Suitable for a wide range of applications, including agricultural
- Environmentally Friendly: Uses less energy in manufacturing and can be designed
Description
A fabric building is a type of structure that uses fabric, usually made of durable materials like polyethylene, PVC, or other synthetic textiles, as its primary exterior covering. These buildings can be used for a variety of applications, including agricultural storage, industrial facilities, sports complexes, and event spaces.
Key Features of Fabric Buildings:
1.Structure: Fabric buildings typically have a frame made of steel, aluminum, or other materials, which supports the fabric covering. The design can be temporary or permanent, depending on the intended use.
2. Lightweight: The materials used in fabric buildings are generally lighter than traditional building materials, making them easier to transport and install.
3.Versatile Designs: Fabric buildings can be customized in size, shape, and layout to fit specific needs, making them suitable for a wide range of functions.
4. Natural Lighting: Many fabric structures allow for natural light to enter, reducing the need for artificial lighting and creating a more pleasant environment.
5. Cost-Effective: They can be more affordable to construct and maintain than traditional buildings, particularly for large spaces.
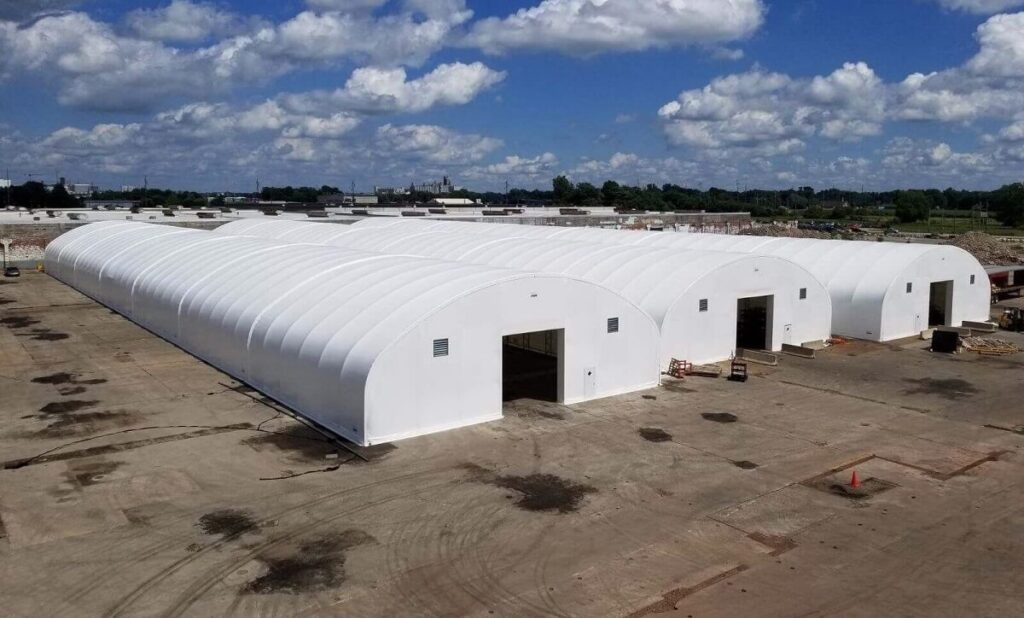
Advantages of Fabric Buildings:
1. QuickInstallation: Fabric buildings can often be erected in a shorter time frame compared to conventional structures, making them ideal for urgent needs.
2. Energy Efficiency: He insulation properties of certain fabric materials can help maintain temperature, potentially reducing heating and cooling costs.
3. Durability: High-quality fabric can withstand different weather conditions, including wind, rain, and snow, depending on the design and construction.
4. Flexibility: Fabric buildings can be designed to be demountable, allowing for relocation or reconfiguration as needs change.
5. Low Maintenance: Thesestructures typically require less maintenance than traditional buildings, and the materials are resistant to corrosion.
6.Sustainability: Many fabric buildings can be designed with eco-friendly materials and practices in mind, contributing to sustainable construction efforts.
7. Enhanced Airflow: The design often promotes better ventilation, which can be beneficial for certain applications, such as agricultural uses.
Applications of Fabric Buildings:
Agricultural Use: Storage forhay, equipment, and livestock shelters.
Industrial Use: Warehousing, manufacturing, and workshop spaces.
Recreational Use: Sports facilities, gymnasiums, and event venues.
Commercial Use: Retail spaces, showrooms, and temporary structures for events. Overall, fabric buildings offer a versatile and efficient solution for a wide range of applications, combining functionality with cost-effectiveness.
Safety of Fabric Buildings:
Fabric buildings can be safe and durable when designed and constructed properly. Here are some key aspects of their safety:
1. Structural Integrity:
* Fabric buildings are typically supported by a strong frame made of steel or aluminum, which can withstand various loads, including wind and snow.
* The design should comply with local building codes, which consider factors such as wind speed, snow load, and seismic activity.
2. Material Quality:
* High-quality, durable fabrics (like PVC or polyethylene) are used, which can resist tearing, UV degradation, and weathering.
* Fabrics are often treated to be flame retardant, adding an extra layer of safety.
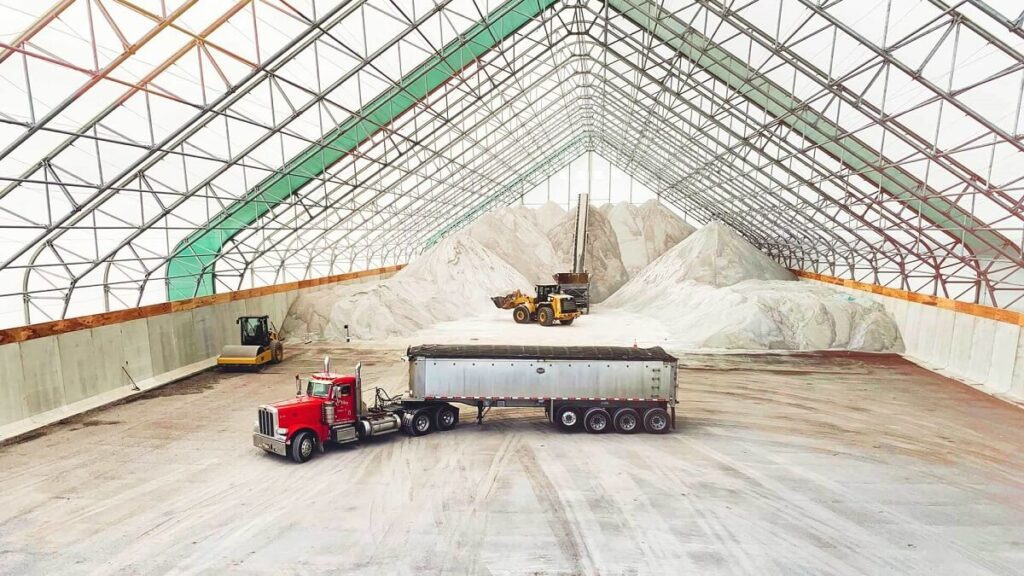
Analyzing Fabric Structures with 3D3S Software:
3D3S is a specialized software tool used for the analysis and design of structures, including fabric structures. Here’s a step-by-step guide on how to analyze fabric structures using the 3D3S software:
Step-by-Step Analysis Process
1. Model Creation:
* Define Geometry: Start by creating the 3D model of the fabric structure. This can include defining the overall shape, dimensions, and layout of the fabric cover and structural frame.
* Input Nodes and Elements: Specify points (nodes) and connect them with elements to represent the fabric and supporting framework. For fabric structures, this often involves tensioned membrane elements.
2. Material Properties:
* Assign Materials: Define the properties of the materials used in the structure: * Fabric Material: Enter parameters such as tensile strength, elasticity, and thermal properties.
* Frame Material: Specify the properties of the structural frame materials (e.g., steel or aluminum).
3. Load Definitions:
* Dead Loads: Input the self-weight of the fabric and the supporting framework.
* Live Loads: Include other loads that might act on the structure, such as occupancy loads or equipment.
* Environmental Loads: Apply relevant loads such as: * Snow Loads: Based on local building codes and snow accumulation data.
* Wind Loads: Consider wind speed and direction, applying appropriate coefficients based on the structure’s geometry.
4. Boundary Conditions:
* Support Conditions: Define how the structure is supported. This may include fixed, pinned, or sliding supports at various points.
* Tensioning: If applicable, specify tensioning conditions for the fabric, as tension is critical for its structural performance.
5. Meshing:
* Finite Element Meshing: If the software requires it, generate a finite element mesh for the model. This divides the structure into smaller elements for analysis.
* Element Types: Choose appropriate element types for fabric (e.g., membrane elements) and the supporting framework (e.g., beam or shell elements).
6. Set Analysis Parameters:
* Static or Dynamic Analysis: Choose the type of analysis you want to perform. Most fabric structures will undergo static analysis, but dynamic analysis may be necessary for certain conditions (e.g., wind loading).
* Load Combinations: Set up load combinations according to relevant design codes to evaluate the worst-case scenarios.
7. Run the Analysis:
* Execute Calculation: Start the analysis process. The software will compute how the fabric structure behaves under the applied loads and conditions.
* Monitor Progress: Check for any errors or warnings during the analysis run.
8. Results Interpretation:
* Displacement Analysis: Assess the displacement results to ensure they are within acceptable limits.
* Stress Distribution: Analyze the stress results to identify areas of high stress or potential failure points.
* Support Reactions: View the reactions at the supports to ensure they are manageable and within the design limits.
9. Optimization:
* Modify Design: If the results indicate issues (e.g., excessive deflection or stress), make design changes. This may involve adjusting the geometry, selecting different materials, or changing the tensioning system.
* Re-run Analysis: After modifications, re-run the analysis to confirm improvements.
10. Documentation:
* Generate Reports: Compile a detailed report summarizing the analysis process, findings, and any design recommendations.
* Visual Outputs: Include visualizations such as stress contour plots, displacement diagrams, and load path diagrams to effectively communicate results.
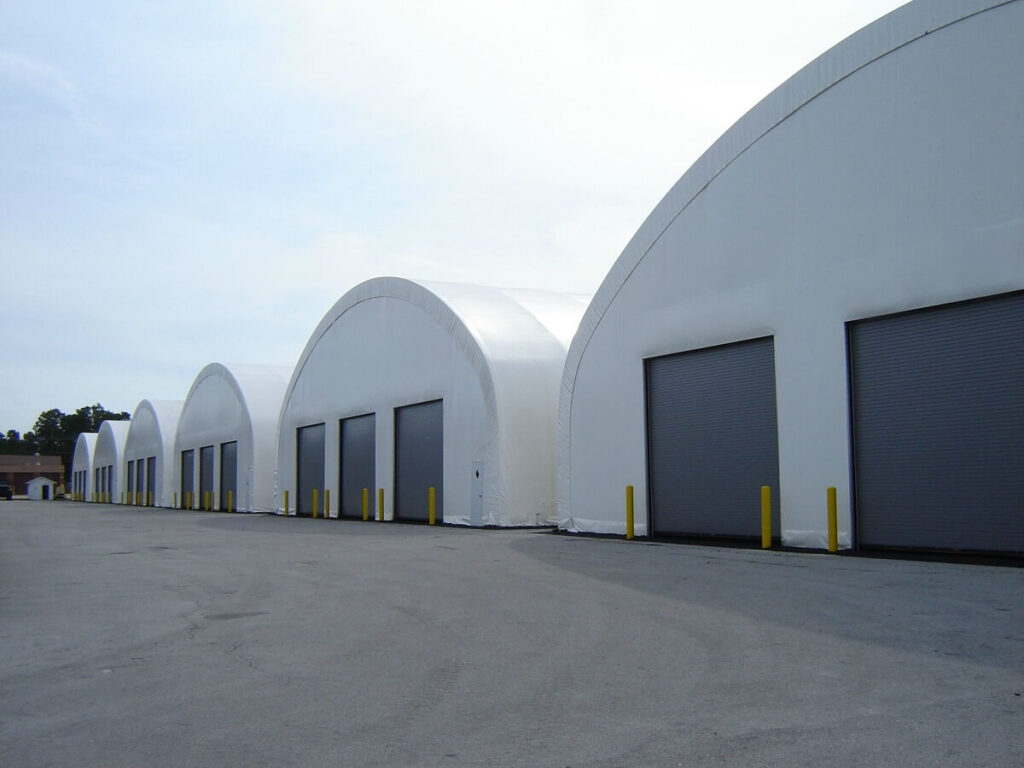
Hot galvanizing is a process used to protect steel from corrosion by coating it with a layer of zinc. This is achieved by immersing the steel in molten zinc at a temperature of around 450°C (842°F). The zinc reacts with the steel to form a series of zinc-iron alloy layers, providing a durable and protective coating.
Advantages of Hot Galvanized Steel
1. Corrosion Resistance: The zinc coating provides excellent protection against rust and corrosion, extending the lifespan of steel structures, particularly in harsh environments.
2. Durability: Hot galvanized coatings are tough and resilient, able to withstand mechanical damage and environmental stressors.
3. Maintenance-Free: Once galvanized, steel components require little to no maintenance over their lifespan, reducing long-term costs.
4. Cost-Effective: While the initial cost may be higher than untreated steel, the long-term savings from reduced maintenance and longer service life can make hot galvanized steel more economical.
5. Environmental Protection: The process is environmentally friendly, as the zinc used is recyclable, and the coating process does not produce harmful byproducts.
6. Adhesion: The metallurgical bond between the zinc and steel provides a strong, long-lasting coating that adheres well to the base metal.
7. Aesthetic Appeal: Hot galvanized steel typically has a clean and attractive finish, making it suitable for visible
applications.
FAQs
Yes. Customized logos can be printed on the tent fabric according to your requirements.
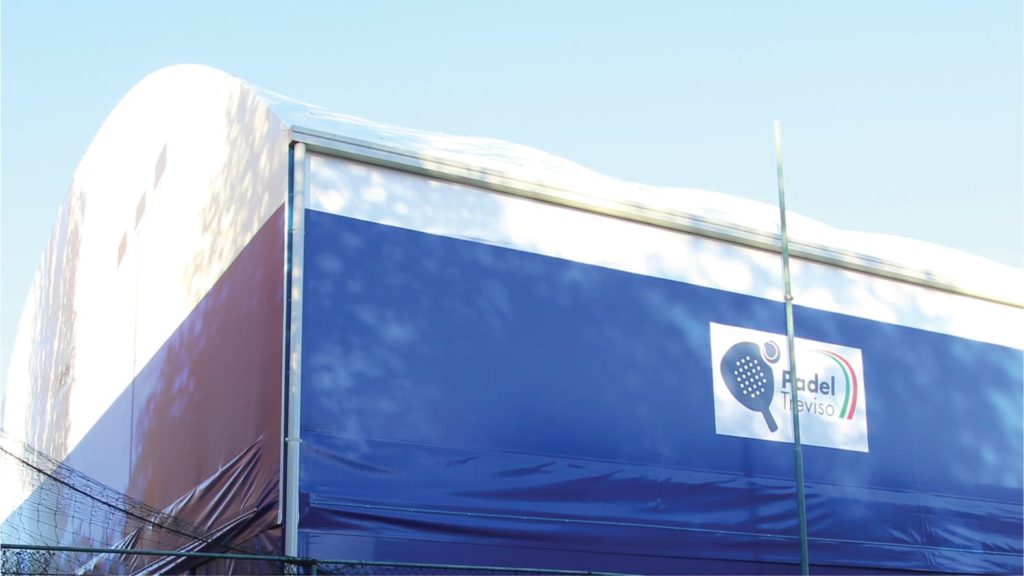
Yes. We assure you all prices are based on factory. We are an experienced tent factory, providing competitive prices, direct quality control, and flexible production scheduling. Our factory has 2 advanced welding robots, 8 welding machines, 2 shearing machines, 10 punching machines, 4 bending machines, 2 sinking machines, 2 heat sealing machines, 10 sewing machines and many professional production workers. In order to assure high quality products and services to customers, all of our operations are strictly conducted in accordance with the ISO 9001: 2008 quality control systems.
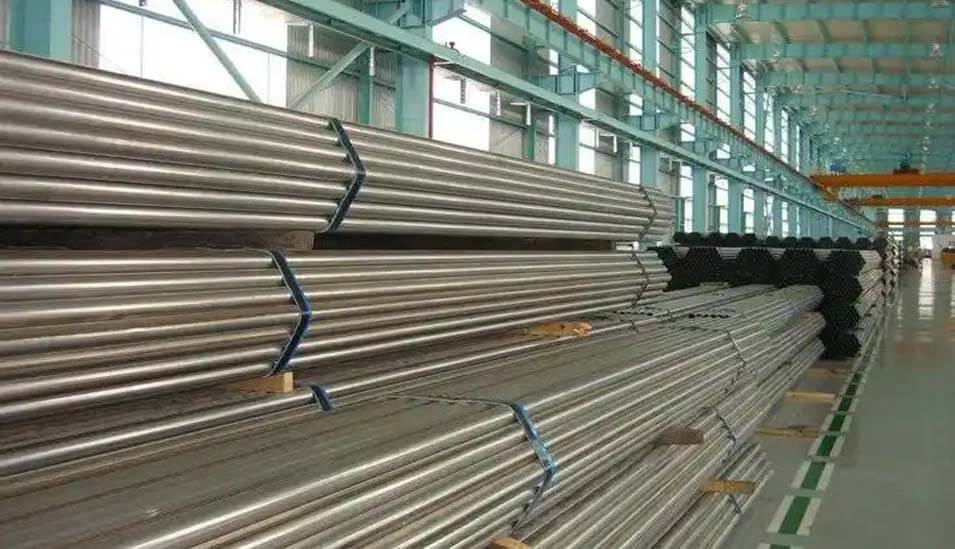

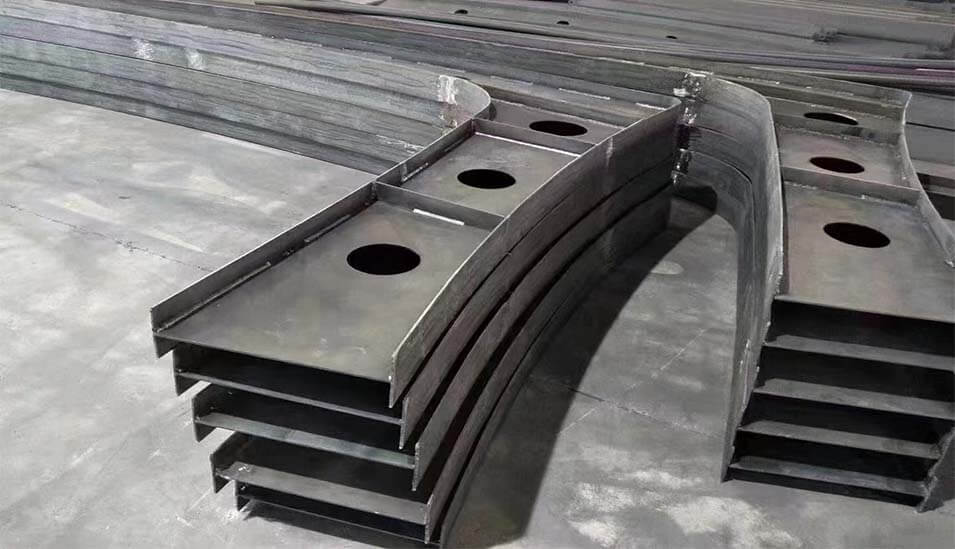
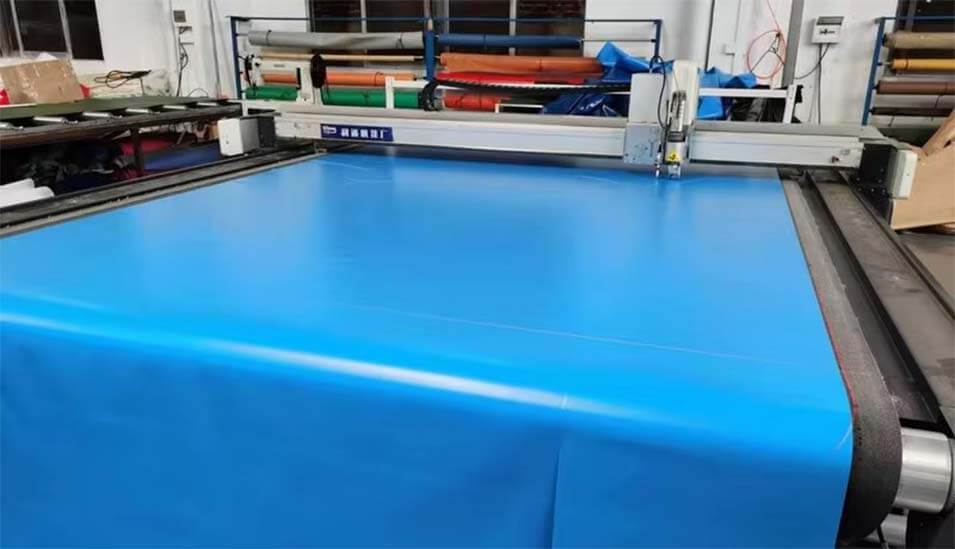
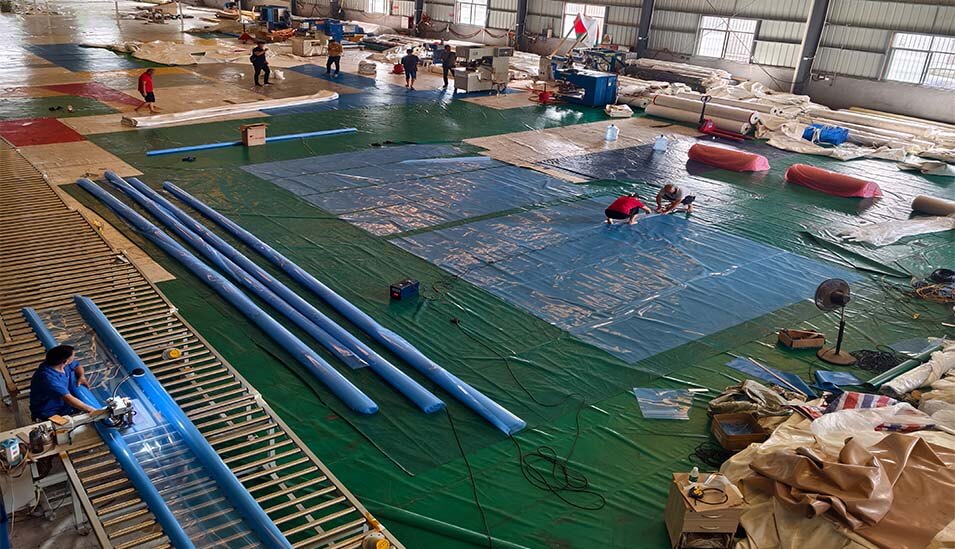
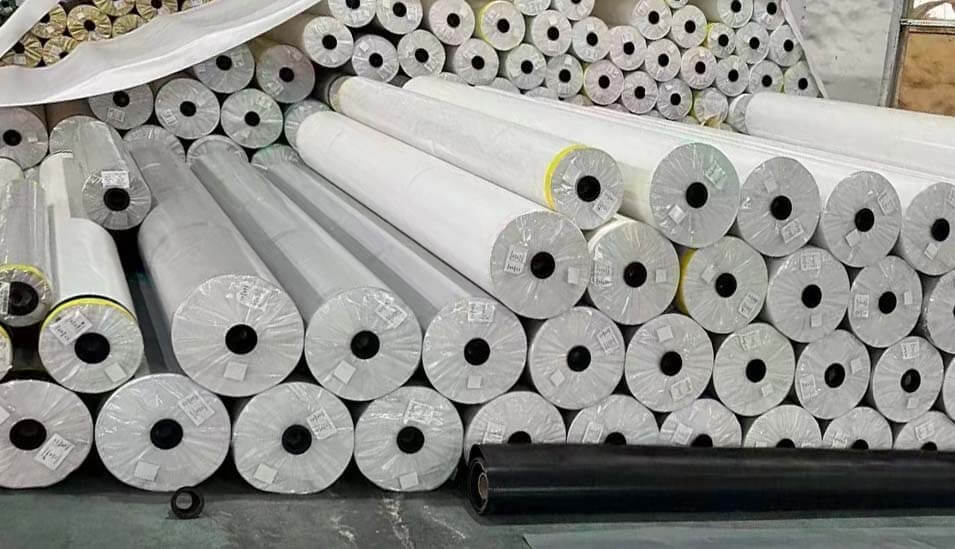
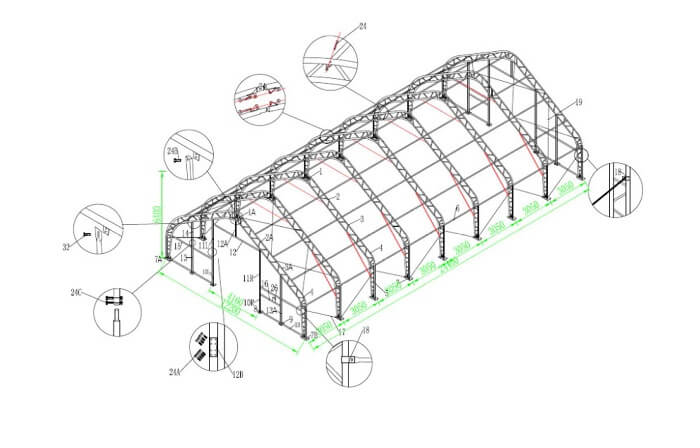
Our tents can be assembled and dismantled easily and repeatedly with small transportation size. The lifespan of aluminium framework can reach 15-20 years, and 5-8 years for PVC fabrics depending on different conditions of usage.
A full range documents including structural drawings, packing list, installation manual and relative certificates can be provided. Moreover, customs declaration is provided. We provide one-stop service for you.
You can contact with our sales team, telling us what kind of event you are going to hold, and how many people you are going to accommodate. We will offer a suggestion according to your event usage and required capacity.
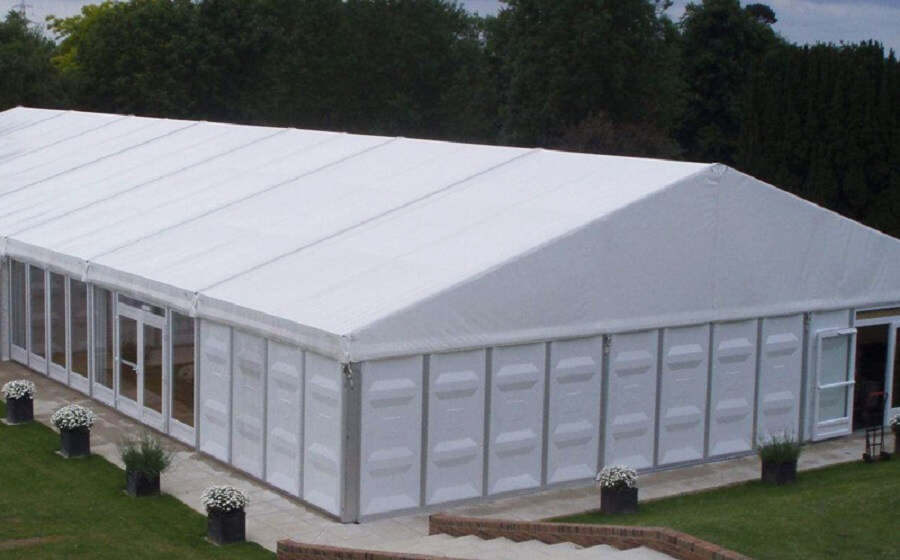
Regular size tents will take about 25-35 working days after receiving deposit. You can contact Zhongke team to further discuss based on the specific tent and quantity.
REQUEST A QUOTE
RELATED PRODUCTS
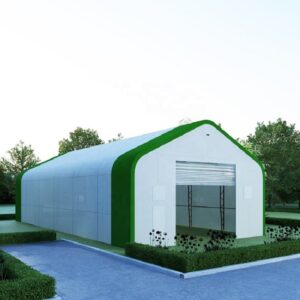
Prefabricated Workshop Canopy Steel Structure Farm Storage Tent Warehouse Metal Shed
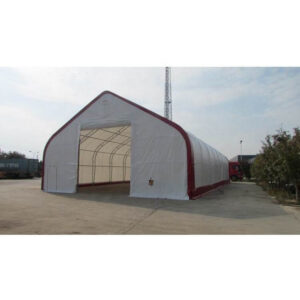
Double truss frame agricultural industrial big peak warehouse storage building
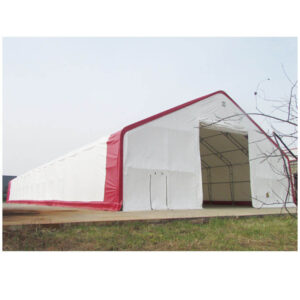
Waterproof heavy duty double truss fabric industrial storage building tent
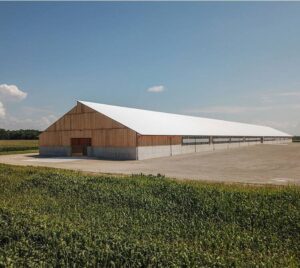